.png?width=300&name=1%20(2).png)
Inozyme Pharma swaps out complicated eQMS for a better-fitting solution
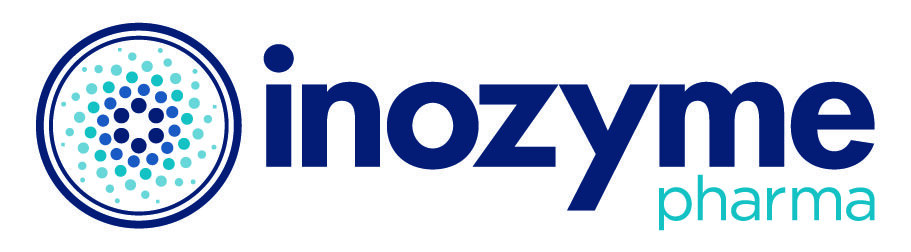
About Inozyme Pharma
Inozyme Pharma, Inc. (Inozyme) is a clinical-stage rare disease pharmaceutical company developing novel therapeutics for the treatment of diseases impacting the vasculature, soft tissue, and skeleton. Inozyme is developing INZ-701, an enzyme replacement therapy, to address pathologic mineralization and intimal proliferation, which can drive morbidity and mortality in these severe diseases. INZ-701 is currently in clinical development for the treatment of ENPP1 Deficiency, ABCC6 Deficiency and calciphylaxis.
Success Highlights
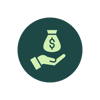
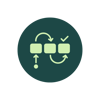
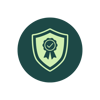
Performing a root cause analysis…on the existing eQMS
Imagine spending tens of thousands on an electronic quality management system (eQMS), only to continue relying on paper and manual processes, even after implementation. That’s exactly how Inozyme’s new VP of Quality and Compliance, Christian Phillips, and his team were managing their existing eQMS. “When I first joined Inozyme, I remember being surprised to learn that a rather sophisticated eQMS platform had already been implemented two years prior. I wasn’t used to seeing systems of that magnitude and complexity at small companies like ours, still very early in clinical development.”
The system Inozyme had in place was a well-known and well-established eQMS. However, for a company whose processes were still in development, lack of easy reconfigurability and an intuitive interface created a mismatch.
“It was very rigid and inflexible, particularly when it came to reconfiguring workflows within the system,” said Christian. “Even small modifications typically required assistance from the platform provider, often with lengthy turnaround times and additional costs. We were spending more time trying to navigate the system than performing the work it was intended to support and streamline. We had to develop hybrid approaches, utilizing paper at times to capture all of the relevant information to ensure traceability and adequately demonstrate Quality oversight and decision-making.”
Christian’s team spent several months determined to get to the root of the issue, enlisting guidance and support from the vendor’s in-house customer support team as well as outside consultants, leading to cost overruns. In the end, these efforts still failed to solve the problem.
“We tried for months until we finally realized that a complete rebuild was necessary,” said Christian. “The ‘tweaks’ we made over time intended to alleviate constraints often led to greater holistic challenges. We weren’t able to maintain the vendor’s full engagement to ensure a holistic approach to the issues, so we continued to spin our wheels for some time.”
Ultimately, Christian realized that the platform itself was not the right fit for Inozyme. Inozyme needed a fit-for-purpose, intuitive eQMS platform that could be easily modified to meet the growing needs of the organization and its ever-evolving operations. They found it in ZenQMS.
No paper? No problem!
Not having every input item or process ironed out, and not putting things down on paper before entering them into ZenQMS took Christian some getting used to, but now he appreciates the flexibility.
“I was hesitant at first because of our experience with [the previous eQMS]. I knew we didn’t have everything fully baked at launch, and sure enough, while working through our first deviation with the new system, I thought, ‘I wish we set up the workflow differently.’ But the new system was much more intuitive and within a day, we had independently modified the deviation workflow configuration to meet our needs. With ZenQMS, there’s no need to figure things out on paper first. You can jump right in, and you should!”
Perhaps the biggest advantage that Inozyme realizes with ZenQMS is the configurability that the platform offers them. As a rapidly-growing company operating in the rare disease space, their processes are constantly being refined. The rigid eQMS they were hampered with before simply couldn’t meet their needs.
“ZenQMS has been a lifesaver for us. You can open a change control to modify the configuration to meet the needs of an evolving quality system and operation, and you can do so without having to rely on the service provider. ”
The results speak for themselves
Configurability aside, the implementation of ZenQMS at Inozyme has led to immediate and tangible benefits for Christian and his team:
Enhanced Document Control
ZenQMS dramatically improved the management of their standard operating procedures (SOPs) and Quality documentation, providing the control necessary for rapid development cycles, typical in the rare disease space.
“A year ago, I couldn’t give you an accurate list of effective controlled documents within our eQMS because there were too many conflicting reports being generated by the system depending on how the query was entered. We have foundational control now that we can further build upon, and we were able to get it almost immediately with ZenQMS,” said Christian.
Cost Savings
ZenQMS proved to be more affordable than Inozyme’s previous eQMS, not only in terms of base costs, but also by eliminating the unforeseen costs associated with having a mismatched system to begin with.
“We paid outside consultants who had direct expertise with the platform to try and deconvolute the old system and reverted to paper systems in the interim. Anytime we needed to make a change, we were completely reliant on the vendor, which incurred additional costs. Pulling the plug and going with ZenQMS was an easy decision for myself and our senior management team.”
Increased Compliance
With the implementation of ZenQMS, Inozyme Pharma has significantly enhanced its compliance capabilities through system-wide visibility that helps them provide holistic Quality oversight to the operation, facilitating the ability to identify and mitigate Quality risks.
“Being able to train on SOPs couldn’t be easier with ZenQMS,” said Christian. “It’s not a black box, it’s all right there for you to see and it’s very intuitive. Does it have all the bells and whistles of the other system? No, but that’s by design. If you overengineer your eQMS, you actually compromise and undermine your ability to maintain compliance and provide meaningful Quality assurance. With ZenQMS, we have compliance right out of the gate.”
If you’re struggling with a complicated quality system that’s not fit-for-purpose, schedule a demo with ZenQMS and find out how we take the stress out of eQMS.