.png?width=300&name=1%20(2).png)
ZENQMS’ VERSATILITY ALLOWS AEROSPACE MANUFACTURING COMPANY FORMLOGIC TO BECOME MORE FUNCTIONAL AND EFFICIENT

About Formlogic
Formlogic is a precision manufacturing company located in Pittsburgh, PA, specializing in automated production of custom components for the Aerospace and Frontier industries. With a customer base long held back by slow-moving supply chains, Formlogic sets itself apart by providing clients with key advantages like speed and efficiencies of scale, all while remaining compliant with AS 9100 and ISO 9001 standards.
Success Highlights
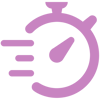
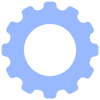
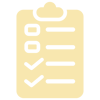
Business Need
When Formlogic was first established, speed was the key. In an industry slow to change, they wanted to get moving fast and revolutionize their industry. They did what many companies do at first - they relied on a home-grown paper-based quality system to get to market faster and limit early costs. It served its purpose for a time, but when Formlogic’s growth and future prospects could not be sustained without upgrading to an electronic quality management system (eQMS), they made a move that would better prepare them for the future.
“Paper is an easy way to get started, but it sure as heck isn’t an easy way to continue to manage and grow!” said Michelle Merwin, Director of Quality Assurance. “We had document control and document approval routings that were literally checklists on paper, and I would run around the factory to get signatures completed in a timely fashion.”
In order to scale, Formlogic needed a more efficient way to keep processes like document control, training, records, and vendor approvals organized, and more importantly, compliant with AS 9100 and ISO 9001 standards for the Aerospace industry. However, their search for an eQMS designed to match those standards was more difficult than they anticipated.
“We looked at other products, some of which were much more complex with features that were overkill for our needs,” said Michelle. “Some had built-in systems that were geared specifically toward the AS 9100 standard, but were actually missing portions of the standard or had links that pointed to a black hole.”
Michelle booked a demo with ZenQMS, with an eye towards finding the simplest way to configure and achieve compliance. “Sometimes less is more,” said Michelle. “ZenQMS didn’t claim to be specifically built for AS 9100 compliance. What it claimed to have was document control, training, and user workflows…and that’s exactly what we use it for. Not having a million bells and whistles is more efficient for us. It makes it easier to use, easier to learn, and we’re not paying for a bunch of features we don’t need.”
Business Impact
The versatility of ZenQMS and its lack of rigid templates made it easy for Michelle and her colleagues to create useful, aerospace-specific workflows that matched their processes while still staying compliant.
“I love that I have the ability to add custom fields. In Aerospace, you have to look at human factors when you’re doing root cause analysis. So within the corrective action workflow that we built, there’s a standard set of human factors incorporated into one of our custom fields. I can populate them with what’s important to Formlogic and use them throughout our different workflows, whether it’s a non-conformance, a corrective action, or a continual improvement report.”
Configurability is crucial for a precision manufacturer like Formlogic. Their small but agile team would be brought to a standstill if they continued to depend on manual systems, paper forms, and wet ink signatures. With ZenQMS, Michelle can adapt quickly and create processes that make her job easier.
“We built a workflow for general and facilities improvements to better manage change. It’s a checklist of all the environmental, safety, and quality components that we would consider in order to control a process, like a major machine installation for example, without adding any unnecessary risks. I also built a workflow to manage our raw material process. It’s a loop that goes from procurement all the way to release for manufacture, and includes a custom field with our approved vendor list. It’s a built-in stop-gap that helps keep everything in control. It’s great that we can upload our material traceability and certification documents to each record; and link the record to its associated work orders.”
By moving to ZenQMS, Formlogic was able to quickly implement a strong foundation for their quality system, all while staying compliant with AS 9100 and ISO 9001 standards. They are now able to be more efficient, productive, and can maintain more control over their documents and processes than they ever could with their previous manual solution.
“Zen allows us to grow and scale easily because we’re not chasing down those records anymore. I can pull up my dashboard, see what’s outstanding, and follow up immediately without having to hunt through a mountain of paper,” said Michelle.
Believe it or not, those benefits aren’t hard to come by. There’s a misconception that quality system implementations need to be complicated and lengthy. That’s simply not the case with ZenQMS. Formlogic was able to get their system implemented quickly thanks to ZenQMS’ customer success team, who supported Michelle and her colleagues throughout the process and made it possible for them to get started even though they didn’t have a huge Quality team.
“We needed something in place so that we could become more functional, quickly. I’d recommend ZenQMS for anyone hoping to get into an eQMS quickly because that’s where their team really shines. Getting started was so easy. They were always there to answer questions, provide learning examples, and supported system validation to get our system set up rapidly.”
If you’re looking to make the move to an eQMS that values simplicity and versatility, schedule a demo with ZenQMS and learn how we can make your job easier.