.png?width=300&name=1%20(2).png)
ZENQMS HELPS BOSTON BIOPRODUCTS ACHIEVE ISO 13485 AND ENHANCE ITS QUALITY MATURITY
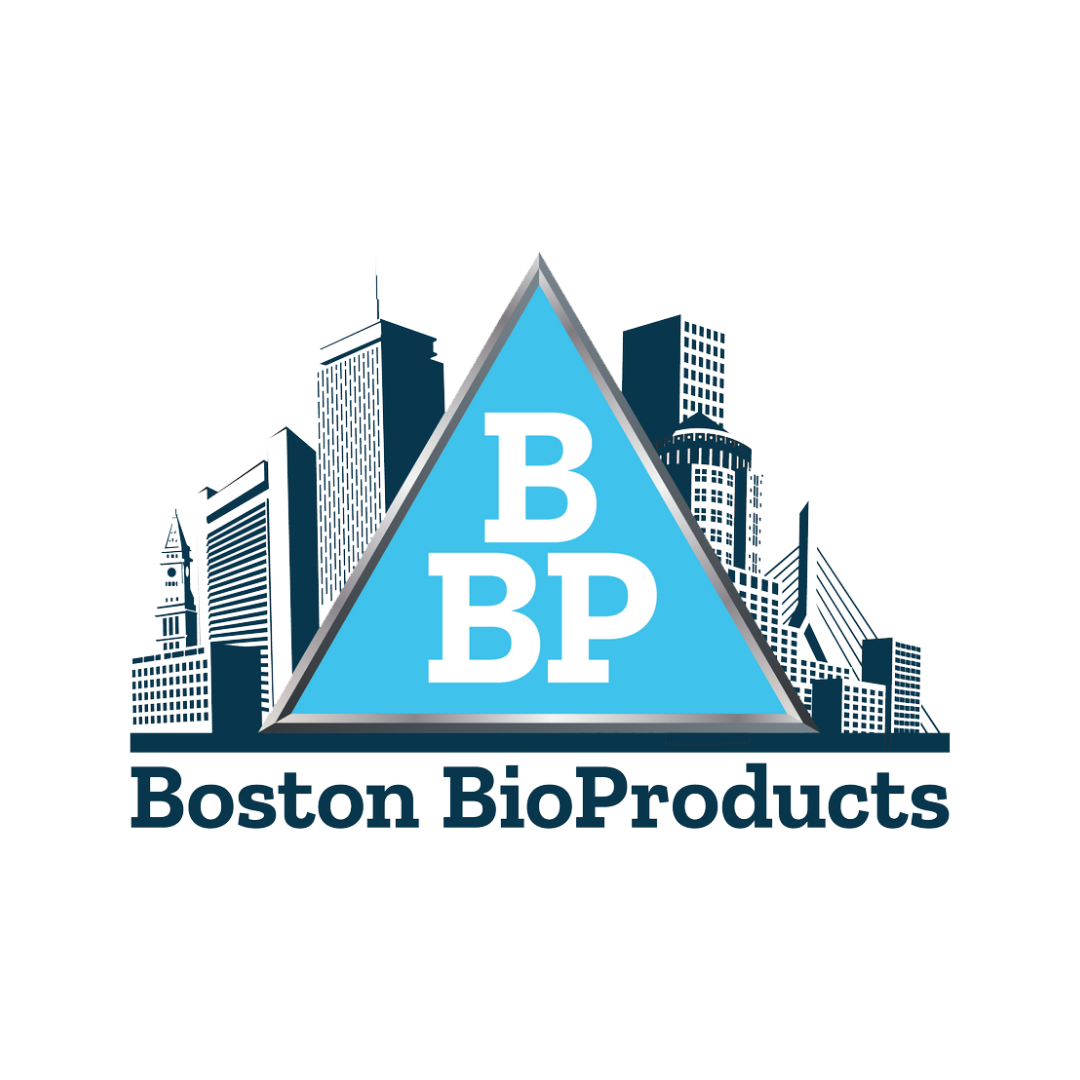
About Boston BioProducts
Established in 1995, Boston BioProducts (BBP) manufactures and delivers a comprehensive range of biological buffers, solutions, culture media, and flexible custom reagent manufacturing services to the biotech industry, CDMOs/CROs, diagnostic and tools developers, and academic researchers.
Success Highlights
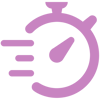
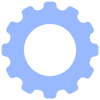
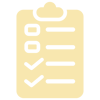
Business Need
The name of the game in buffer manufacturing is speed. In General Manager Neil Sharma’s words, “They aren’t a material you plan for. They’re something you needed yesterday.” With accelerated lead-times and excellent customer service as the standard, the team at BBP have transformed the family-based manufacturer of biological buffers for academic research facilities into a major commercial supplier supporting labs globally.
This change didn’t happen overnight. Even before the COVID-19 pandemic created higher demand for life science products and service offerings, BBP was already planning an expansion.
“Our base was primarily non-GMP academic customers whose priority was product performance,” said Neil. “Our goal was, ‘Let’s get our product to them as soon as possible.’ As we started growing, the need for larger scale manufacturing, comprehensive quality control testing, and a mature quality management system became evident in order to meet regulatory expectations and customer needs.
To reach those customers, the team at BBP made the decision to prepare for ISO 13485 certification, the internationally standard for quality management systems (QMS) specific to the medical device industry. Boston BioProducts felt achieving this 3rd party certification was critical to becoming an approved source of supply to larger, GMP-focused prospects. However, embarking on the robust ISO 13485 certification process without a scalable electronic quality management system (eQMS) to help enforce and manage the quality system and related processes presented an intimidating challenge.
“Our historical quality software served its purpose, but up-revving documents was a nightmare. And when we realized the amount of documents we’d need to up-rev for ISO 13485, it was going to be a huge project,” said Neil.
Process Development Lead Vincent Chan had other requirements. “When I came to BBP, I was tasked with supporting the revamp of their quality system to prepare for ISO 13485. The quality system we chose needed to fit our process. Also, it couldn’t require a full team to constantly monitor it.”
Price was also a concern. “Some of the systems we looked at, their pricing was significantly higher. Implementation costs were prohibitive to get started, and pricing only would increase as we scaled as a business, including additional costs as we added more employees,” added Neil.
He was very clear when he outlined the reasons for opting for ZenQMS. “The training features were superior to other solutions, our entire company could access the system, and ZenQMS was far more affordable. It was almost night and day.”
Business Impact
Along with the benefits mentioned above, Neil and his team have been impressed with all the additional ways, intended and otherwise, that ZenQMS has helped them succeed.
“With ZenQMS, our document up-revving process has been cut down from a week to one hour, and that’s not an exaggeration,” said Neil. “For a company like ours, where we’re wearing multiple hats, that time is huge. I’m working alongside our Production and Quality teams to update work instructions and preparing for internal quality audits as well as ISO 13485. I had to make sure I made room for other critical projects.”
Since moving off of their historical eQMS, Boston BioProducts is able to better serve a more complex and demanding set of customers and achieve a higher quality standard, while maintaining the fast lead-times (with both quality and manufacturing) that customers expect when working with BBP. Along with increased efficiency on the document management side, ZenQMS allows BBP to achieve a level of self-sufficiency that has expanded to include their audit prep, production, and training compliance.
“ZenQMS has helped build a quality culture,” said Neil. “With our old system, we were limited to four users at a time. When we got ready for audit prep, we had to have one of our quality members download the docs, work on their PC, and then ask someone to log off,” said Neil. It was a nightmare. Now, everyone is doing everything at the same time.”